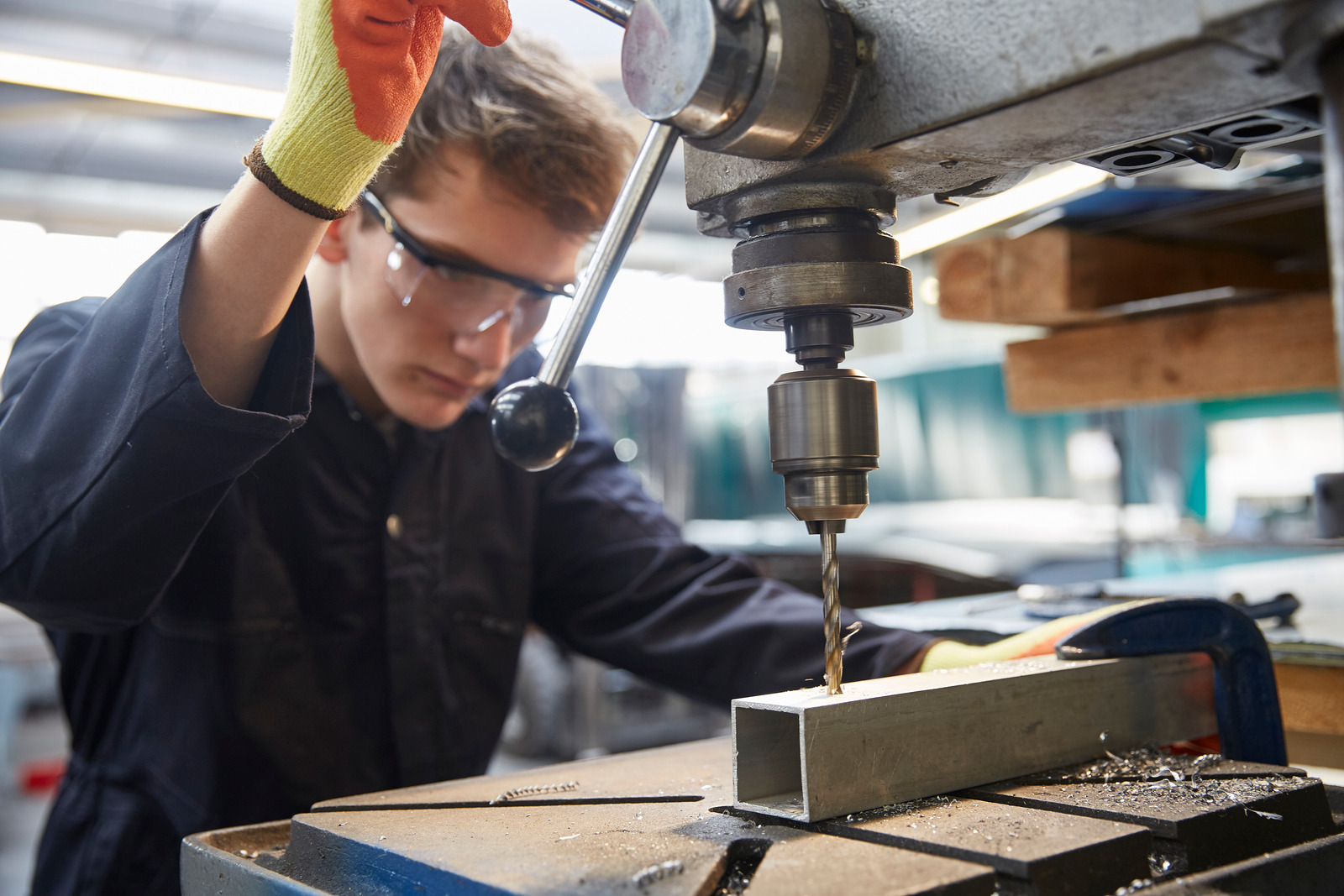
Understanding the Steel Fabrication Process: From Design to Delivery
Structural steel can be found in many different industries all over the world, from the skyscrapers that grace big cities to the frames of your car.
These are made using steel fabrication, which turns simple steel into strong, reliable steel structures that can be used for many products and projects.
But how does steel fabrication work? This article will explore how professional steel fabricators carry out the process of converting raw steel into a wide variety of shapes and components used in countless industries.
Types of steel used in steel fabrication
There are many types of steel used in steel fabrication.
The most used is carbon steel due to its affordability, strength and formability.
Other popular options include stainless steel, which is highly resistant to corrosion, and high-strength steel, which is used for structures that are required to withstand heavy loads.
Tools used in steel fabrication
The steel fabrication process involves multiple specialised tools, including:
- Saws: These come in many shapes and sizes, from band saws for smaller cuts to torches for thicker materials.
- Welding Machines: Metal arc welding is the most common option, while Tungsten Inert Gas is also a popular choice.
- Press Brakes: Powerful machines that are used to bend and shape the steel.
- Computer Numerical Control Machines: Automated machines that can create complex shapes and perform repetitive tasks accurately.
The steel fabrication process
The are numerous stages involved in the steel fabrication process.
The initial concept phase involves designing projects using computer-aided design drawings with detailed specifications and calculations.
Once the design has been finalised and the preferred material has been selected, the steel fabrication process can begin.
The first step is to cut the steel to the desired lengths. This can be done by hand but is often done using CNC machines. The steel is then shot blasted to remove any impurities.
Following this, the steel is bent into shape using press brakes. Bending allows for straight, rigid shapes as well as curved edges, and prevents the steel from breaking when used.
The next step is to manufacture the steel to the design specifications. This can involve anything from piercing holes to trimming excess metal or creating specific shapes on the steel.
The steel is then welded. This involves melting materials which, when cooled, will be attached. Welding is essential in ensuring the stability and strength of the steel.
The final stages involve quality checking and finishing (adding extra layers of protection) before the steel is assembled, delivered and installed.
Global Engineering are expert steel fabricators offering services across NZ. To find out more, visit our website today or contact our high-calibre team.